传统齿轮的加工通常采用湿切方法。
随着机床、工具、材料的发展,高生产效率、高精度、节能、环保、低成本齿轮制造成为现实。美国科研机构开始研究齿轮干切技术,在进行研究后,使得该技术得以推广应用。在应用过程中发现干切齿轮加工对机床、工具的耐热、耐磨性能要求高,齿轮加工企业的投入成本高。对现有齿轮加工设备而言干切加工方法并不具有实用性。可现有齿轮加工企业面临提升加工效率,降低生产成本、改善环境等方面的问题。而微量润滑技术不仅可以取代传统齿轮加工时切削油润滑方式,还能在加工效率、降低生产成本、改善环境方面有明显的优势。滚齿加工国外一般采用如下技术路线:提高切削速度,缩短切削工具与工件间的接触时间,使切削热由切屑带走。
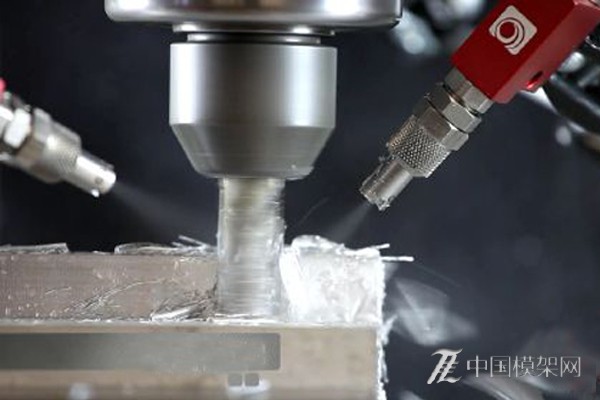
微量润滑技术之所以能够在齿轮加工中取得不错的应用效果,是因为微量润滑采用的是超细油雾粒子渗透至切削区域,提供良好润滑油膜,抑制切削摩擦热的产生,降低切削力,提升加工效率,避免了湿切状态下滚齿时各齿反复受到的热冲击引起的微裂纹产生,导致的切削工具寿命降低的问题。
滚齿加工基本原理:在齿轮加工中通常设置3个喷嘴将微米级油雾颗粒喷射至切削区域,其中有一个喷嘴保持一定距离对滚刀前刀面喷射油雾润滑,使滚刀在进入切削时能有油膜,起到抑制温升、降低滚刀磨损、防止粘连和提高工件加工质量和切削工具寿命的作用。
微量润滑滚齿应用现场案例数据如下:滚齿线速度约110m/min;成本节约30%以上
齿根圆直径(mm) | 法向 压力角 | 法向模数 | 齿数 | 材料 | 油品消耗 | 电力消耗 |
62.97 | 20° | 4.233 | 17 | 20CrMnTi | 3ml/个工件 | 3W |
结论:
(1) 滚齿切削过程中切削刃口—切屑、切削刃—工件间由于摩擦作用形成的毛细管是润滑油渗透的主途径。微量润滑系统形成的雾粒直径小,速度高,渗透性好,能够起到更好的润滑作用。
(2) 切削过程中的摩擦作用是影响切削力的主要因素之一,微量润滑有效渗透至切削区的能力,良好的润滑效果降低了切削过程中的切削力。
(3) 相比传统切削及干切削,微量润滑切削可有效控制切削工具磨损的进程,延长切削工具使用时间。
(4) 由案例数据可知,微量润滑油的消耗量很低。