通过对TD处理工艺各阶段的控制,提高了冲压件的品质,降低了企业经营成本。目前开发的新车型高强度钢板模具的压边圈、凹模镶件(左/右纵梁后部、左/右A柱下加强板、左/右B柱上部横梁)已全面普及TD处理工艺,以后计划在高端车型的高强度钢板模具开发方面,尝试使用更高级别的ASS?AB88材料,并同步开展TD处理工艺与ASSAB88母材适应性的研究。
随着我国汽车工业的高速发展,各大主机厂对汽车安全性的关注度也越来越高。通过在车身安全结构件中使用高强度钢板替代普通钢板,以提高车身的安全性,势必对模具零件强度、耐磨性提出更高的要求。高强度钢板在R角及复杂成形面处极易出现毛刺缺陷,该缺陷已成为阻碍冲压件成形质量提升的难题,通过引入模具TD表面强化技术,可以提升冲压件成形质量和延长模具镶件的使用寿命,具有制造成本低、整改周期短的特点。
TD工艺简介和工艺流程
TD工艺简介
TD模具表面强化处理技术是热扩散法碳化物覆层处理(thermal diffusion carbide coating process),在一定的处理温度下将零件置于硼砂熔盐及特种介质中,特种熔盐中的金属原子与模具零件中的碳、氮原子发生化学反应,扩散到模具零件表面而形成膜厚几微米至几十微米的钒、铌、铬、钛的金属碳化层。实践证明,这种覆层厚度为10~15μm,硬度达到2800~3200HV,具有很高的耐磨性、抗崩刃性、耐蚀性,可以重复TD处理3~5次。
高强度钢板模具材料的选用逐步使用高耐磨、抗崩刃的SKD11替代Cr12MoV,合资品牌在尝试使用更高级别的模具材料ASSAB88(材料成本是SKD11的2倍以上),高强度钢板材料对比数据如表1所示。
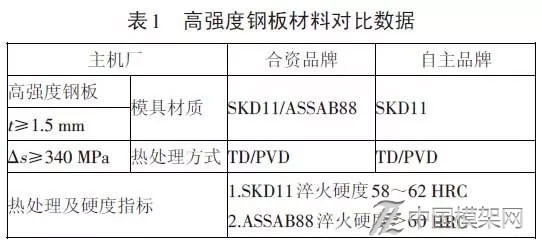
TD工艺流程
① 来料检查:镶件数量、质量、外观(碰伤、裂纹等)、母材牌号、母材硬度检测和确认;
② TD处理前尺寸和硬度确认(零件长宽尺寸不能大于620mm×850mm);
③ TD处理前打磨和抛光(粗糙度小于Ra0.8mm);
④ TD处理:预热(520℃左右)、TD处理(900~1030℃硼砂熔盐8~12h)、盐浴淬火(500℃左右盐浴10~20min)、回火2次(低温回火180~200℃,高温回火500℃,回火时间在3~5h);
⑤ 清洗及孔中盐类物质去除;
⑥ TD处理后尺寸和硬度确认;
⑦ 尺寸调整确认;
⑧ TD处理后的抛光;
⑨ 出货检测(碰伤、裂纹、杂质、硬度、皮膜厚度);
⑩ 包装出货。
TD处理前要进行预热的目的是防止镶件产生剧烈变形和开裂,预热温度设定为520℃左右,以保证镶件表面不产生氧化物为前提。需要注意的是镶件从硼砂熔盐到盐浴中的速度要快,以防止TD层氧化。
TD处理的使用范围
TD处理适用于汽车冲压成形类模具的镶件、各种挤压模、滚压模、弯管模、成形模、弯曲模、扩口及缩口模、变薄拉深模等。
TD处理的优点
模具镶件通过TD处理后,可以提高其表面的耐磨性和母材的韧性,通常情况下进行TD表面处理后,其使用寿命至少提高8倍以上、冲压单件合格率能提升到98%以上、停线时间缩短、维护成本降低。
TD处理模具零件选择
一、Cr12钢材不适合做TD处理,因为TD处理后,相关技术参数不达标:①模具零件硬度不达标,一般只能达到45HRC左右,耐磨性较差;②零件尺寸变形大,Cr12在TD处理过程中没有二次硬化,由材料自身的特性决定的。
二、油钢(DF2)、碳钢类不适合做TD处理,因为其热处理工艺不适合TD处理工艺要求,油钢、碳钢的淬火温度在780~850℃,而TD的淬火温度在900~1030℃。
三、高速钢不适合做TD处理,高速钢TD处理属于二次淬火过程,开裂风险大,而且热处理工艺与TD工艺不适应,高速钢淬火温度为1200℃左右,而TD的淬火温度在900~1030℃。
四、不锈钢系列钢材不适合做TD处理,因为含碳量低,在0.1%~0.3%,TD处理后无法成膜(要求母材含碳量在0.3%以上)。
TD处理常见问题及应对措施
一、模具零件在TD处理过程中,会出现母材硬度不足,尺寸无法调整的问题,主要原因是模具母材牌号错误或质量达不到相关标准和要求;应对措施是选择适合TD处理的优质模具钢,例如:SKD11、Cr12MoV。
二、模具零件TD处理后会出现焊接部位不成膜或存在裂纹的问题,主要原因是:TD处理前模具镶件R角和成形面存在较明显的裂纹和砂眼缺陷、焊条材质与母材不相融(热膨胀系数和收缩率相差较大)、焊接工艺不合理等。针对镶件R角和成形面缺陷(裂纹和砂眼)的应对措施是首先使用砂轮机和磨头将缺陷部位表面深度0.5mm以下去除,然后选择与母材相融的焊条实施焊接、修磨、抛光。对于已实施过TD处理的模具镶件,需在200℃左右的加热炉中保温1~2h后再实施焊接,这样可以减少开裂风险,提高焊接质量。
为了筛选出最适合母材的优质焊条,通过试验数据验证不同型号的焊条在SKD11上焊接后,实施TD处理的效果(膜厚和硬度指标)。
试验材料
①母材:材质为SKD11;
②焊条:包括CMC-EMagic6、TM2000在内的6种不同型号焊条。
②焊条:包括CMC-EMagic6、TM2000在内的6种不同型号焊条。
试验步骤
①由具有丰富经验的模具高级技师,依次使用6种不同型号的焊材在母材上试焊3cm长的焊接面,并做好1~6的编号(见图1);
②将焊接面表面打磨光滑,实施TD处理;
③TD处理完毕检测膜厚、硬度参数,观察其外观,并做好记录,检测数据如表2所示;
④依据评价标准,对6种不同型号的焊条焊接后的TD效果实施综合评价。
②将焊接面表面打磨光滑,实施TD处理;
③TD处理完毕检测膜厚、硬度参数,观察其外观,并做好记录,检测数据如表2所示;
④依据评价标准,对6种不同型号的焊条焊接后的TD效果实施综合评价。
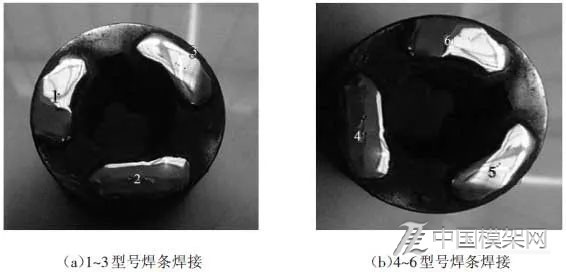
图1 TD处理图示
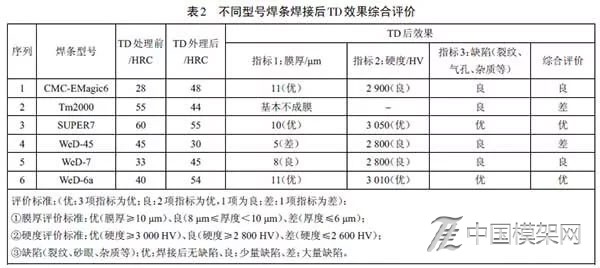
试验结果
使用型号3(SUPER7)和型号4(WeD-6a)焊条在SKD11母材上焊接,TD处理后效果(皮膜厚度、硬度、外观质量缺陷参数等)最优;上述试验数据是通过试验得来,不同的施焊人员、焊接设备、焊接方法、不同批次的焊接母材和焊条、焊接环境、检测设备等,得到的检测数据可能有偏差。
三、模具镶件经过多次TD处理后,会引起模具零件表面成膜不好、耐磨性差或开裂的问题,主要原因是模具零件经过多次TD处理后母材表面的碳原子含量会逐渐减少,皮膜厚度不断下降,同时母材表面脱碳层越来越深;如果母材表面脱碳层深度达到0.50mm以上,TD处理后模具镶件表面成膜效果较差,严重时会引起镶件开裂,当出现以上缺陷时,则不再适合做TD处理。
TD处理变形量控制
一、冲模镶件实施TD处理过程,实际是二次淬火的过程,其组织变化与真空淬火后的组织变化基本相同;不同的是TD淬火的介质和真空淬火的介质。
真空淬火的介质是油和氮气,在常温下这2种介质在零件淬火时冷却速度较快、热应力释放也较大。在这种情况下如果保护不当,会引起零件的变形和开裂;通常情况下,真空热处理的变形量比TD处理的大,且开裂风险增大。
TD淬火的介质是等温盐浴,盐浴淬火温度控制在500℃左右,淬火时间10~20min,零件在此过程中冷却速度较慢,释放出的热应力较小,一般TD处理后的模具镶件整体变形量和开裂风险都较小。
二、变形量的控制要求:平面和侧面的变形量可以控制在±0.05mm左右。当前行业内对于零件变形量的控制参数,参照日本行业相关标准,冲模镶件尺寸长、宽、高均在300mm以内的控制在±0.10mm左右,在100mm以内的控制在±0.05mm,在50mm以内的控制在±0.03mm,特殊要求除外。