今年5月,大连机床董事长陈永开因涉及一起亿元级别的骗贷案件被公安部通缉,令行业震动。而陈永开执掌的大连机床,也在2017年9月就因为涉嫌骗取江西省某金融机构6亿元贷款,被公安部门立案侦查。
比案件更令人瞩目的是,大连机床的悲惨结局:因高达224亿元人民币的债务总额,于2017年11月被法院裁定破产重整。
想当初,一提中国的机床就是沈阳、大连、秦川这几家,有那么几年,沈阳机床规模第一,大连机床效益最好。
虽然这几年机床行业不景气,但外资厂商和一些国内企业日子过得还是不错的。作为行业龙头的大连机床烂成这样子,这是难以想象的,更难想象的是,烂成这样的机床企业,不只大连机床。
更令人唏嘘的是,陈永开还先后获得“2003年度辽宁省十大财经风云人物”、“2005年全国机械工业优秀企业家”、“2005年度辽宁省劳动模范”、2006年“第三届中国工业经济年度十大风云人物”等荣誉称号。
2015年9月,现在看来已经是大连机床内忧外患的岁月,陈永开还在高调地给自己赞歌,称大连机床每年都要投入5亿左右的研发费用,并且已经通过 “借船出海”“弯道超车”,从中国“制造”跃向了“创造”。
【1】
【1】
大连机床集团是老牌的国有企业。它的前身为始建于1948年的广和机械工厂,1953年改名为大连机床厂。1995年11月,以大连机床厂为核心,合并了大连市机床工具行业的主要企业,组建了大连机床集团。
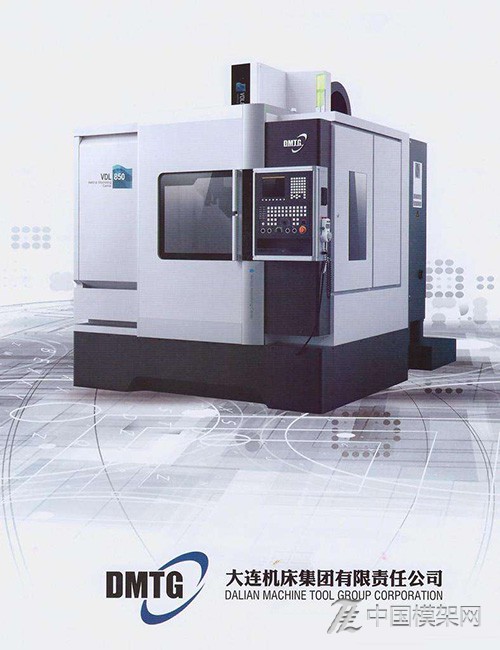
2000年至2006年,该公司连续7年获中国机床工具行业销售收入、数控产值、出口创汇、精心创品牌四项"十佳"企业称号。2004年大连机床的DMTG品牌数控机床获中国名牌产品,2006年它甚至在世界机床工具行业排行榜上名列第8位。
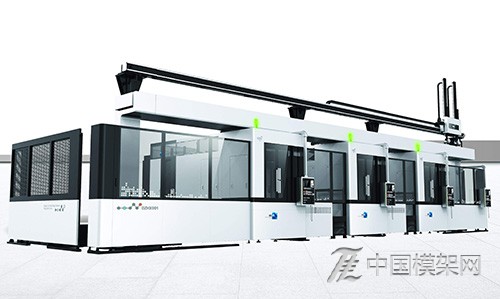
2004年初,大连市政府要求大连机床只保留20%的国有股权,其余80%向社会资本转让。随后几经股权变更,大连机床完成股改,名义上变为国有参股的民营企业。但其股权结构究竟如何,始终如迷雾一般让人捉摸不透,即使业人士也不十分清楚。
直到2013年华东数控向大连高金科技公司增发5000万股,其预案公告才透露,大连高金董事长兼总裁陈永开是大连机床的实际控制人。
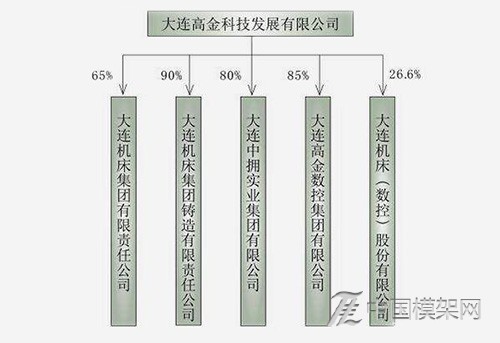
2004年大连机床改制,2006年大连机床达到顶点开始转走下坡路。
虽然由国企转为民营,但大连机床的经营模式仍保留了国企作风,倾向于选择风险相对较低的成熟技术和成熟产品,创新激励不足,大量技术人才、管理精英流失,整体产品创新和研发能力一步步弱化。
机床行业的十八罗汉,本应为国家研发高精尖及替代进口产品,这些年里却大多在中低端产品中相互拼杀,不断推出价格战,以近乎卖铁的价格卖机床。
大连机床以普通机床和经济型数控机床等中低端产品为主,技术壁垒薄弱,市场门槛低。随着市场需求逐步转向高端数控机床,中低端机床市场供过于求,该公司过去的低价策略不再有效,收入逐渐下降,整体毛利率仅能维持在10%的低水平。
大连机床也有意转向技术和创新的竞争战略,走中高端产品路线。为此,它从2006年开始不断扩大投资,改造原有生产线。虽然投钱不少,但实际效果并不好。
同时,该公司的存货积压问题十分突出,存货余额在流动资产中的占比长期处于50%的平均水平。2016年月末,大连机床存货高达79亿元,较2015年增加了13%。再加上数亿元的应收款,大连机床的盈利变现效率严重恶化,资金链紧张,最终导致债券连续违约。
但导致大连机床垮掉的原因不仅仅如此。
像很多“不务正业”的企业那样,大连机床过度涉足金融投机,直接影响了企业产品、服务的更新换代和创新研发。
对于大连机床来说,其市场支配地位和“准国企”角色,使得它比一般企业更容易拿到低成本融资,让其有足够本钱去资本市场折腾。
在国内炒楼热潮一浪高过一浪,大量实体企业把资金投向楼市的时候,大连机床就热衷于此。在旅顺占地16万平方米的楼盘“中拥海山花苑”,投资方即为大连机床集团。
大连机床集团旗下还拥有全资、合资、控股及参股子公司有40多个。在国内股票二级市场,大连机床集团亦有涉足。
很早之前,高金科技就一直想要将旗下的机床资产包装上市,曾欲借华东数控之壳让大连机床上市。2013年,高金科技出资3.2亿元认购了5000万股华东数控普通股,持股16.26%,成为华东数控第二大股东,距离控股股东仅一步之遥。但因高金科技负债累累,持有的华东数控股份全部被司法冻结等一系列原因,距离上市一步之遥的大连机床最终借壳失败。
【2】
【2】
工业水平看装备制造业,装备制造业水平看机床。机床行业作为装备制造业的核心和基础,为制造各类专用及通用设备提供工艺装备,是衡量一个国家制造业水平高低的重要标志,是一个国家的工业产品保持国际竞争力的重要保证。
尤其是高精、高细、高速、柔性、智能、生产工艺高度集成的数控机床,作为国家战略性产业的重点发展领域,它不仅关乎工程机械、汽车、电力、铁路等一系列行业,还要为航空航天、舰艇潜艇、火箭直升机等国防领域提供精密制造装备。
2002年入世后,中国步入经济发展黄金期,也成为全球第一大机床消费国和生产国,生产了大量中低端机床。
但自2011年开始,受全球经济低迷影响,我国机床市场也一蹶不振,成本高、价格低、利润低成为了机床行业的一般趋势。大多数机床公司都是在微利下求生存,行业价格战愈演愈烈。
面临经营危机的机床厂家不在少数。
除了大连机床,汉川机床也黯然落幕,上市公司华东数控面临倒闭。“烈士榜”上还有长征、济一、杭机、联强、三一、耀发,名不见经传的小厂倒闭的更是数不胜数。
行业老大沈阳机床,也是凭借共和国机床长子的招牌,在资本运作和债务处理上左右出击,一边逼着供应商签署债务豁免协议,一边拉着国家相关部委为自己的融资背书,才勉强A股保壳。它还不得不抛弃上市子公司昆明机床,任其被中止上市交易,令人唏嘘。
据业内统计,从2011年起,机床行业的营业收入及利润总额增速持续下行,行业亏损企业数量由2011年的359家增至2016年的818家,亏损金额由2011年的15.99亿元增至2016年的72.77亿元。
从2017年开始,国内机床行业景气度有所回升,当年机床行业利润总额同比增长192.6%,其中金属加工机床利润总额更是同比增长579.7%,但全行业亏损企业占比仍达33.8%。而且从行业整体看,技术水平有限、同质化严重、产能过剩、低价竞争的局面并没有改变。
【3】
【3】
虽然中低端机床市场惨不忍睹,但相对来说,垄断了国内高端机床市场的外资厂商还是很滋润的。
这些年,国内进口了大量的高端机床,早已是全球第一大进口国。
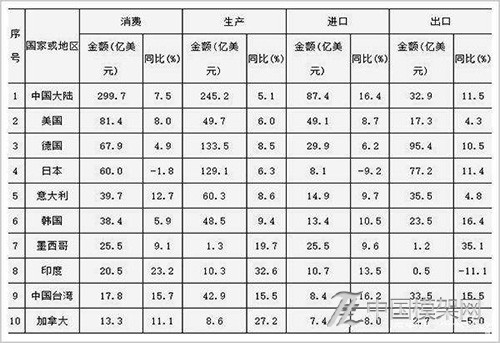
▲2017年全球机床消费前十名的国家和地区情况—— 数据来源:美国Gardner商业媒体
是本土厂商不能生产高精度机床吗?
能,当然能,但前提是不计成本。
国内机床厂由于不掌握整机设计、制造和使用的核心技术,缺乏自主研发和创新能力,关键部件受制于人,产品质量问题突出且缺乏竞争力。
在很多业内人士看来,高端数控机床我们的水平比德国、瑞士、日本等国相差了几十年,国内产品市占率不足5%;中档数控机床,与上述国家及我国台湾地区也难以匹敌,而且80%的国产机床的核心部件和数控系统要依赖进口。
这背后到底是什么原因?
机床行业是工业母机,重要性毋庸置疑。但多年前机械、机电部就被裁撤了,相关的基础研究一直都非常薄弱。
在组成机床的零部件中,数控系统、伺服驱动、转摆头、高速主轴、刀具、丝杠,导轨、量仪等核心部件,基本都要依赖进口。
自己做吧,要么做不出来,要么能做出来但成本比国外产品的市场价还贵,而且可靠性、精度保持性很差。不自己做吧,又怕被国外掐脖子。
以车床主轴为例,普通车床要求其主轴的跳动要求不超过0.02毫米(2丝)。这种精度的轴承,代表国内最高综合水平的哈轴(哈尔滨轴承集团)、瓦轴(瓦房店轴承集团)、洛轴(洛阳轴承集团)也能生产,但如果要求长时间保持这个精度(3年甚至10年)就做不到了。

至于好点的机床,其主轴跳动往往不能超过0.003毫米(3μ),就更难了。
高端的零部件我们技不如人,也就罢了。可很多看似普通的东西比如气缸、密封件,国内也做得不好需要进口。
汽缸,原理很简单,但台湾一支行程150的带导轨气缸就要2000元人民币。
SKF大塑料密封圈,800规格的要3000多。
刀具这样重要的消耗品,更是必须从山高、住友、维尔特这些国外厂商进口。亏我国还是钨粉的生产、出口大国,高端刀具却必须求助于外国供应商。
极端情况下,国内机床厂只做床身、立柱等结构大件和一些辅助配件,所有其他核心功能部件全部依赖进口,机床厂只是将这些零部件进行组装、调试和销售,成为名副其实的机床组装厂。
可即便是机床床身所用的铸件材料,我们与国外的差距恐怕也不是几米,而是十几层楼高,严重影响机床精度及性能。
所以有人感慨:我们除了厂房,其他都是进口。
国外厂商也倾向于将数控系统和伺服驱动、电机、主轴等关键部件打包销售,部分高精尖产品还不给我们,甚至进口产品的现场调试过程也要保密,拒绝国内技术人员参与。
机床生产是个综合性很强的行业,涉及冶金、材料、物理、化学、电气、加工、工艺、热处理、微电子、数控技术等各个领域。任何一个环节出问题,都会影响整体性能。
国家投巨资攻关机床核心部件,却没能有效解决基础性短板,大量功能部件被德国、日本、瑞士、美国控制,不仅每年要花费大量外汇,更危及国家工业经济安全。
没有高质量的国产功能部件,还谈什么机床强国呢?
国外厂商之所以技术研发和创新能力强,很重要一点在于非常注重技术攻关、产品开发、市场营销等各个环节密切协作,遵循做好基础知识储备和人才保障才能拥有源源不断的技术创新的理念。
反观国内厂家,过分追求短期效益和利润最大化,即使有能力也不把做好做精产品当做第一目标。它们或者实行所谓多元化战略,搞“大而全”的经营模式,造成资金链断裂;或者急功近利,大搞“资产经营”,缺少卧薪尝胆、持续提高机床产品加工精度和可靠性的决心和耐性。
除了已经破产的大连机床和负债累累的沈阳机床,还有很多企业为此付出惨重代价。
上世纪80年代,济南第一机床厂(济一)为日本马扎克公司来图制造车床,并由日方出口美国。这种合作模式对济一的工艺技术要求极高,如齿轮噪音,不仅考核分贝数,还要听了“悦耳”,标准不可谓不苛刻。但在时任厂长朱锡泉的带领下,经过艰苦努力,一个个难题都解决了,出口势头良好。
可后来的继任者认为此类合作监督太严、挣钱不多而不愿再做,解除了与马扎克合作。此后济一引进技术又出现决策失误,逐渐衰落。
再比如上海机床厂(磨床的研发与制造)和昆明机床厂(生产测量装置),在解放后曾为发展精密机床发挥了重要作用,如今都失去了光芒。特别是昆明机床厂作为上市公司(ST昆机),甚至为避免因连续亏损而面临的退市风险,通过虚增收入进行财务作假,被上交所终止股票上市交易。
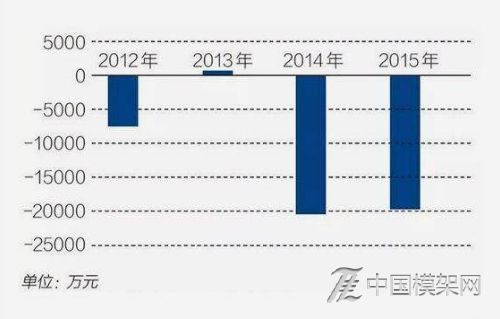
▲昆明机床近年归属于上市公司股东的净利润——数据来源:网易财经整理
相比之下,国外知名的机床企业,很多走的是“专、新、精、强”的路子。
瑞士高精度镜面磨床制造企业Studer公司,几十年来都保持三四百人的员工规模,仅有一座四层楼的厂房。但它的技术呈现飞跃式发展,从手动、半自动、自动、数控,到磨削中心,一步一个脚印,至今仍雄踞世界第一。我国知名的机床企业就用Studer磨床磨削主轴,质量就是好,成为一张王牌。
国内也有心无旁骛、专注主业的机床厂。
济南第二机床厂(济二)在国内机床行业就比较鹤立鸡群。从建厂以来它一直以压力机及龙门刨为主导产品,几十年来除在改革开放以后把龙门刨改为龙门铣外,一直坚持自己的发展方向。
上世纪八十年代济二引进英国威尔逊公司的压力机技术,并进行消化吸收创新,装备了国内几乎所有汽车厂。
在装备国内自主品牌、合资品牌汽车企业的同时,济二生产的大型成套成线产品相继赢得美国福特汽车、日产美国工厂、日产日本九州工厂和法国标致雪铁龙索肖工厂的订单,实现了进入发达国家市场的突破。
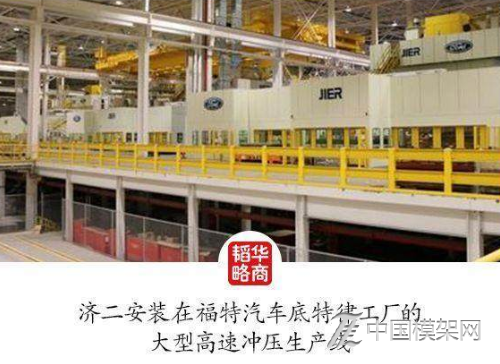
济二生产的大型高架式五轴联动高速镗铣加工中心,可加工各种铝合金、复合材料以及黑色金属等复杂曲面零件的五轴加工,满足航空航天、轨道交通、汽车模具等重点行业大型复杂曲面加工需求,填补了国内空白。

几十年来,济二经受了多种考验,在“做大”、“多元化”、“合资”浪潮中没有迷失方向,不断积累在压力机设计、制造方面的经验代代相传,也没有对国内外企业实施兼并,仅依靠自己的力量发展成为能与世界顶尖的压力机企业,与德国的Schueler及Weingarten进行竞争。
但像济二这样“引领技术,引领市场”的锻压机床企业实在太少了。
此外,在人才培养和技术积累方面,企业的表现也差强人意,大把的资金用于扩大生产规模、上项目,用于设计研发的实验室、研发室的投资却少之又少。
在国内,机床这行又苦又累还不体面,待遇也低,设计人员、工艺人员、技师的工资比不上那些售楼售车的,毫无经济价值可言。大学毕业生不愿选择制机床行业,现有人员也难以沉下心来钻研技术,要么忙于应付项目报告,要么转岗,或被外国同行高薪挖走。这直接造成了年轻中高端技术人才的匮乏和企业技术研发的断档。
同时,在一些人看来,虽然机床行业的研发能力比上世纪80年代强了很多,但某些方面也退化了不少。80年代国内可没有现在这么先进的设计软件、仿直软件,图纸全都是手工绘制。翻看当时的手工画图,水平之高让人佩服。
同时,在一些人看来,虽然机床行业的研发能力比上世纪80年代强了很多,但某些方面也退化了不少。80年代国内可没有现在这么先进的设计软件、仿直软件,图纸全都是手工绘制。翻看当时的手工画图,水平之高让人佩服。
现在的研发设计人员则完全被商用软件束缚了思维和手脚,尽管软件操作十分娴熟,但对软件背后的力学、电磁学、控制论等基础理论知识缺乏深究,最终也无法研制出一台好的数控机床。
还有,机床行业没有几十年的经验教训是培养不出一个合格的技术人员与技师的,这个行业需要长期的经验累积才能不断发展。国外机床厂关键工种及装配调试技师都是50多岁以上、怀有绝技的老技师,国内企业呢,早就退休或转岗了。这无疑是对人才的极大浪费。
对于一个企业来讲,流失一、二个精英人才也许还问题不大,可如果放大到全国问题就十分严重了。
人才是创新的基础和核心要素,创新驱动本质上是人才驱动。缺少了规模足够、结构合理、素质优良、技艺精湛的人才队伍,国内机床产业的路能走得远、走得好吗?