现代飞机,汇集当今各种高新技术于一体,被誉为人类现代工业科技之花,航空工业也因此成为各国经济和国防建设的战略性产业,得到了持续和快速的发展,同时也带动着新材料、通信电子等其他高新技术产业尤其是高新制造产业的蓬勃发展。
飞机装配是根据尺寸协调原则,将各零部件或组件按照设计技术要求进行组合、连接,形成高一级的装配件直至整机的过程,是整个飞机制造过程中最为关键的一环。回顾飞机工业的发展,飞机装配技术经历了从人工装配、半机械/半自动化装配到机械/自动化装配的发展历程,而目前得到各经济、军事发达国家高度重视的数字化装配技术,正成为现代飞机制造的科技制高点。
数字化装配技术国内外发展现状
新一代飞机制造为飞机装配提出了日益苛刻的装配技术要求,传统的装配手段已无法满足,具体体现在以下几个方面:
(1)大尺寸框梁骨架装配精度不易保证。
飞机骨架零件的大型化,零件制造及装配过程中的自身大变形,装配过程缺乏有效的检测及控制措施,这些均导致目前的装配手段已无法满足高指标的设计技术条件要求。
(2)复合材料的大量使用带来的制孔质量差、效率低。
飞机大量采用复合材料带来了复合材料的制孔问题。从现有的实际生产情况来看,单纯依靠传统的手工制孔,很容易出现复材分层、孔径椭圆等问题,产品质量无法保证。而大量的大直径、厚夹层(复材+钛合金)结构采用手工制孔,对工人操作技能要求极高、制孔效率低、故障率高,由此带来的质量、进度风险尤为突出。
(3)飞机表面连接件安装质量不稳定。
目前的手工制孔、划窝方式,无法有效保证制孔的法向及划窝深度要求,易出现由于孔位倾斜、划窝深度不准确导致的连接件头部凹凸量超差,影响飞机隐身性能。
面对这些情况,为了保证飞机装配质量,满足机体长寿命要求,同时提高生产效率,数字化装配成为必然的选择,如图1所示。
面对这些情况,为了保证飞机装配质量,满足机体长寿命要求,同时提高生产效率,数字化装配成为必然的选择,如图1所示。
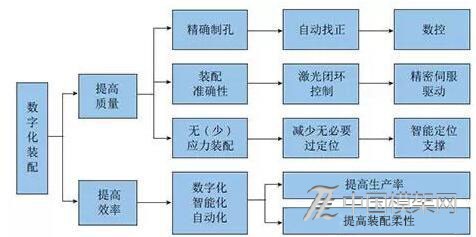
图1 数字化装配技术需求
1.国外现状
自20世纪80年代后期,随着计算机信息和网络技术的飞速发展,以美国波音、洛克希德·马丁公司和欧洲空客公司为代表的大型飞机公司均开始并采用飞机数字化装配技术。波音777、A380、JSF等新型军、民机的生产研制过程,充分体现了国外发达国家飞机制造过程中数字化装配技术的现状和发展趋势。
洛克希德·马丁公司在研制JSF战斗机之初,就提出了将单架生产周期从15个月缩短到5个月,工装从350件减少到19件,制造成本降低50%等指标。为实现这些指标,他们采用了数字化装配手段,取消了75%有关制孔的工具和工装,应用一种先进的龙门钻削系统,采用激光定位、电机驱动进行精密制孔,大大提高了制孔质量以满足飞机长寿命要求,同时也使部件的装配工作节省了90%的时间。
波音公司在787生产的过程中,其结构材料有50%是复合材料,机身的大部段壳体基本上都是复合材料的。考虑到复材机体结构的特殊性,钻孔时材料层间容易劈裂,而且又不适宜敲打,所以它们的连接不能用一般的铆接技术来实现。另一方面,考虑到波音787客机的生产批量大,有数量巨大的孔需要钻制,所以波音和合作伙伴研制了专用的自动化钻孔铆接设备和相关的工艺技术,以此来确保波音787客机的装配连接质量和速率,同时保持低的成本。另外,还在总装过程中采用了iGPS系统,使多用户、大尺度、高精度的测量成为了可能。
空客公司也大规模地采用了数字化的柔性壁板装配系统,集成了电磁铆接技术和柔性装配工装,来解决翼梁大型构件的自动化装配问题。
2.国内现状
国内的飞机装配,虽然在局部上也采用了较为先进的技术,如采用CAD技术进行了包括建立型架标准件库和优化型架及参数设计,对工装、工具和产品的装配过程进行了三维仿真等,开始采用激光测量+数控驱动的定位方式,部分机型还采用了自动钻铆技术等,但总体上与发达国家相比还存在较大差距,具体表现在:
(1)飞机设计制造仍主要采用串行模式,工装、工艺设计与产品设计脱节,制造模式未真正实现到并行模式的转换,导致飞机装配协调困难、返工率高;
(2)尚未实现人机交互的装配仿真以及装配路径的优化;
(3)仍然采用以专用工装为主的刚性定位装配方式,导致飞机制造成本居高不下;
(4)数字化装配应用规模有限,尚未实现一个完整型号真正意义上的全面数字化。
数字化装配技术的应用进展
1.基本介绍
数字化装配技术是一种能提高产品质量、适应快速研制和生产、降低制造成本的技术。数字化装配方法不仅包括了传统数字化装配概念中工装的设计、制造及装配的虚拟仿真等,还包括了如柔性装配、无型架装配等自动化装配方法。飞机数字化装配技术是数字化装配工艺技术、数字化柔性装配工装技术、光学检测与反馈技术、数字化钻铆技术及数字化的集成控制技术等多种先进技术的综合应用。数字化装配技术在飞机装配过程中实现装配的数字化、柔性化、信息化、模块化和自动化,是将传统的依靠手工或专用型架夹具的装配方式转变为数字化的装配方式,将传统装配模式下的模拟量传递模式改为数字量传递模式,其基本工作流程如图2所示。
数字化装配技术是一种能提高产品质量、适应快速研制和生产、降低制造成本的技术。数字化装配方法不仅包括了传统数字化装配概念中工装的设计、制造及装配的虚拟仿真等,还包括了如柔性装配、无型架装配等自动化装配方法。飞机数字化装配技术是数字化装配工艺技术、数字化柔性装配工装技术、光学检测与反馈技术、数字化钻铆技术及数字化的集成控制技术等多种先进技术的综合应用。数字化装配技术在飞机装配过程中实现装配的数字化、柔性化、信息化、模块化和自动化,是将传统的依靠手工或专用型架夹具的装配方式转变为数字化的装配方式,将传统装配模式下的模拟量传递模式改为数字量传递模式,其基本工作流程如图2所示。
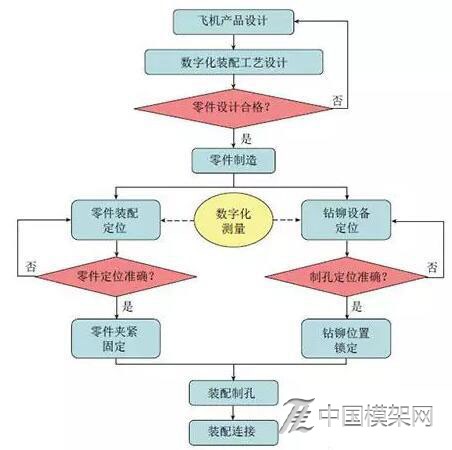
图2 数字化装配工作流程
需要强调的是,数字化装配技术不仅仅局限于软、硬件设备的简单堆砌,更在于融合整个设计、制造的数字化过程,它以产品数据集为中心,以数字量传递为基础,利用数字化装配工艺规划,数控设备的自动钻铆,数字化测量设备的测量定位等技术,使产品在装配过程中真正得到有效控制,建立起一套有效的产品发放过程控制机制以及相关的工作规范和制度,以保证生产效率和产品质量。
2.发展思路
数字化装配技术是飞速发展的各种先进技术综合应用的结果。它的发展和应用是一个长期的过程,由于技术成熟度、应用风险以及资金场地等方面的限制,不可能一蹴而就,需要经历一个由核心技术的突破与应用到数字化装配技术的全线贯通的过程。合理的发展思路是兼顾长远和近期目标,在长期目标的指导下,根据实际情况,由易到难,由点到面,有分解也有综合,基于数字量协调技术、数字化模拟仿真技术、数字化测量技术、软件技术、自动化控制和机械随动定位等先进技术,逐步形成完整的飞机数字化装配集成系统,以实现数字化装配技术的集成应用,真正完成全机数字化装配的目标。
中航工业成飞也以此为原则,本着“现有装配工艺流程基本不变、重点解决装配过程的主要矛盾、系统具有一定的扩产能力、统筹考虑装配工艺布局”的思路,制定了“望尘莫及—望其项背—并驾齐驱”三步走的发展规划,力争2015年在数字化装配领域缩短同国外发达国家差距,在2020年达到国外发达国家的同等水平。
3.技术体系
飞机数字化装配技术体系涉及了装配工艺规划、数字化柔性定位、装配制孔连接、自动控制、先进测量与检测以及系统集成控制等众多先进技术和装备,是机械、电子、控制、计算机等多学科交叉融合的高新技术集成。依据飞机装配的工艺流程,可将数字化装配技术体系归纳如图3所示。
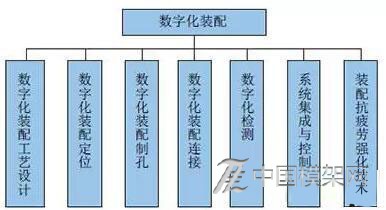
图3 数字化装配技术作用
3.1 数字化装配工艺设计
数字化装配工艺设计的基础是基于模型的定义(MBD)技术,即用集成的三维实体模型来完整表达产品定义信息,作为唯一的制造依据。MBD技术根据数字化定义规范,采用三维建模进行数字化产品定义,建立起满足协调要求的全机三维数字样机和三维工装模型。工艺人员可直接依据三维实体模型开展三维工艺设计,改变了以往同时依据二维工程图纸和三维实体模型来设计产品装配工艺和零件加工工艺的做法,依据数字化装配工艺流程,建立三维数字化装配工艺模型,通过数字化虚拟装配环境对装配工艺过程进行模拟仿真,在工艺工作进行的同时及飞机产品实物装配前进行制造工艺活动的虚拟装配验证,确认工艺操作过程准确无误后再将装配工艺授权发放,进行现场使用和实物装配。在工艺模拟仿真过程中还可生成装配操作的三维工艺图解和多媒体动画,为数字化装配工艺现场应用提供依据。
研究内容主要包括:
(1)数字化精确装配技术体系研究及应用;
(2)基于工艺数字样机的数字化协调研究及应用;
(3)装配容差分配技术研究及应用;
(4)数字化装配工艺流程设计研究及应用;
(5)装配虚拟仿真技术研究及应用;
(6)可视化装配技术研究及应用。
3.2 装配定位技术
装配定位技术主要分为工装定位和零件装配基准孔面自定位两个方面。
装配工装在飞机装配过程中被大量采用以保证进入装配的飞机零件、组合件、板件及段件精确定位。柔性工装克服了刚性工装刚性专用、设计制造周期长、存储占地面积大,结构开敞性较差等缺点,具有柔性化、数字化、模块化的特点。柔性工装具有快速重构调整的能力,一套工装可用于多个产品的装配,从设计、制造、安装到应用均采用数字量传递方式,在硬件上由具有模块化结构特点的单元组成,软件上则包括控制软件、测量软件、装配仿真软件等。全过程的全数字量传递是数字化柔性工装具有高定位精度的重要保证。
传统的对合精加工方式,精度、质量及效率都很难满足新机生产要求,飞机全机大部件对合技术,集机身、机翼、鸭翼、垂尾、发动机和起落架的安装、拆卸功能于一体,能快速、准确地调整各大部件的安装姿态,并带有自动定位和预警提示功能,可有效降低大部件对接过程中的调整难度,减少大部件安装过程中部件的损伤风险。
研究内容主要包括:
(1)重构式柔性工装技术标准化系列化研究;
(2)基于机器人的定位终端执行器系列化研究;
(3)机器人定位集成系统中核心功能部件的标准化和系列化研究;
(4)柔性工装CAE结构分析及优化技术研究;
(5)多层次运动规划与控制技术研究及应用;
(6)柔性工装的数字量驱动数据研究。
3.3 装配制孔技术
现代飞机结构件采用的主要连接方式仍为机械连接,新型飞机高隐身及长寿命特点对改善各连接点的技术状态(表面质量、配合性质、结构形式等)提出了很高的要求,复合材料的大量采用更带来了大量复合材料的制孔需求,单纯依靠传统的手工制孔,很容易出现复材分层、孔径椭圆等故障,产品质量难以保证。尤其是大量的大直径、厚夹层(复材+钛合金)结构制孔,对工人操作技能要求极高,且制孔效率低、故障率高,质量、进度风险尤为突出。解决这些问题的最重要的一个途径,是通过改善制孔工艺方法,采用自动化手段进行连接孔的精确定位和制备,以提高制孔质量和效率。
现代飞机结构件采用的主要连接方式仍为机械连接,新型飞机高隐身及长寿命特点对改善各连接点的技术状态(表面质量、配合性质、结构形式等)提出了很高的要求,复合材料的大量采用更带来了大量复合材料的制孔需求,单纯依靠传统的手工制孔,很容易出现复材分层、孔径椭圆等故障,产品质量难以保证。尤其是大量的大直径、厚夹层(复材+钛合金)结构制孔,对工人操作技能要求极高,且制孔效率低、故障率高,质量、进度风险尤为突出。解决这些问题的最重要的一个途径,是通过改善制孔工艺方法,采用自动化手段进行连接孔的精确定位和制备,以提高制孔质量和效率。
研究内容主要包括:
(1)基于全闭环反馈的孔位找正算法研究及应用;
(2)自动制孔技术研究及应用;
(3)复材部件高性能制孔工艺技术研究及应用;
(4)叠层结构紧固孔超声制孔技术研究及应用;
(5)螺旋铣制孔技术研究及应用。
3.4 装配连接技术
飞机制造中装配连接质量直接影响飞机结构的抗疲劳性能与可靠性。高性能航空器的机械连接结构必须采用先进的连接技术,如采用干涉配合铆接、电磁铆接、新型紧固件、孔挤压强化等来提高连接结构的抗疲劳性能与可靠性,减轻结构重量。而采用自动化或半自动化的连接设备则能显著提高工作效率及连接质量的稳定性。另一方面,先进标准连接件的选取和安装工艺(如安装工具、干涉量的确定等)也应作为装配连接技术研究的重要内容。
研究内容主要包括:
(1)基于柔性机械臂的装配连接技术研究;
(2)自动钻铆机压铆原理与结构技术研究;
(3)电磁铆接技术研究及应用;
(4)干涉连接技术研究及应用。
3.5 数字化检测技术
传统的测量技术已难以满足飞机制造中快速、高效、高精度检测要求,数字化检测技术已成为打通飞机复杂零件与大尺寸零部件设计、制造、装配、检测一体化流程,提升检测效率与水平的关键环节。应采用基于数字化检测设备(坐标测量机、激光跟踪仪、激光雷达、激光扫描仪等)的产品三维检测与质量控制手段,建立数字化检测技术体系,开发计算机辅助检测规划与测量数据分析系统,制定相应的数字化检测技术规范,以实现提高检测效率与质量的目标。
研究内容主要包括:
(1)飞机外形数字化检测技术研究;
(2)飞机水平测量及校准技术研究及应用;
(3)新型检漏技术研究及应用;
(4)基于柔性机械臂的多余物检测技术研究;
(5)基于视觉系统的数字化检测技术研究。
(5)基于视觉系统的数字化检测技术研究。
3.6 系统集成与控制技术
在飞机数字化装配过程中,配套软硬件系统众多,数据处理方式丰富,设计、工艺、测量、定位、制孔、连接等数据间存在大量的交互和协调关系。系统集成与控制技术是实现交互与协调的基础,它将数字化装配技术中各支撑单元即所有自动化装配设备、传感器、测量设备通过通讯网络集成在一起,共享信息,形成一个协调运作的全闭环控制系统。
研究内容主要包括:
(1)数字化装配作业过程集成管理、监测技术研究;
(2)面向数字化装配过程的网络化机电控制技术研究;
(3)机器人系统集成应用平台技术研究。
3.7 装配抗疲劳强化技术
新机除采用优化机构布置,新材料、整体化结构、细节优化设计、结构应力水平控制等设计手段以提高机体结构寿命外,还需采取装配抗疲劳强化技术、长寿命机械连接等措施来满足其长寿命要求。其中,主要的装配抗疲劳强化工艺方法包括滚压、挤压、干涉配合及抛光处理等,而长寿命机械连接则包括高锁螺栓连接、冠状铆钉等。
研究内容主要包括:
(1)开缝衬套冷挤压技术研究;
(2)压合衬套强化工艺研究;
(3)复合强化工艺研究;
(4)电磁铆接强化工艺研究;
(5)高干涉装配连接技术研究。
4.工程应用情况
中航工业成飞紧紧瞄准国外发达国家飞机制造过程中数字化装配技术的发展,结合我国国情和公司的发展规划,在“实现自主创新、提升核心技术和能力”目标的指引下,在数字化装配领域进行了积极并卓有成效的探索,以满足新机装配的如下各项新技术特点。
(1)制孔设备末端负载力大且在较大范围内随加工过程叠层材料和工艺参数不同发生较大变化,严重时呈现非线性动力学特性;
(2)高精度制孔需求苛刻要求制孔装备具有足够的刚性和良好的动态性能;
(3)装配工艺流程具有人工装配和自动装配(制孔)交叉作业的特点。
在具体的数字化装配能力建设过程中,成飞公司通过全面实现装配工艺设计、精确定位、制孔、部件对合与精加工以及检测监控、过程管理的数字化来建立贯通数字化装配生产线和构建完整的数字化装配体系,对数字化装配系统提出了3个“基于”的要求,即基于装配流程以保证工艺继承性,基于测量的数字量协调、传递与控制以保证制造环节的闭环性,基于数模驱动以保证制造依据的唯一性和操作的便利性,最终采用“开放式伺服移动装配定位平台+数控五坐标多作业单元移动龙门制孔机床”的结构形式,分离装配定位系统与制孔设备,实现了人工作业与设备自动作业的解耦。在系统架构方面则采用统一的架构,以确保各项系统架构的一致性,如图4所示。
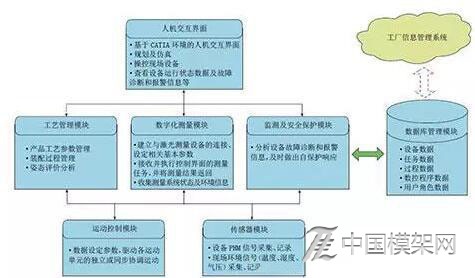
图4 成飞数字化装配系统架构图
数字化装配技术的工程化应用情况如图5所示。
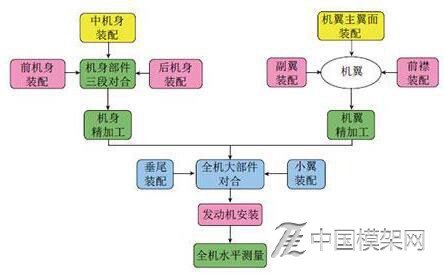
图5 成飞公司数字化装配技术的工程化应用情况
(1)中机身数字化装配系统。
通过采用数字化检测、数控加工、超声叠层制孔、集成管理与控制、误差补偿等技术,开发集工装、测量、数控加工、集成管理与控制为一体的中机身前/后段数字化装配系统,实现中机身前/后段骨架精确定位装配、装配误差在线检测、外覆盖件连接孔精确自动制孔,有效提高了飞机装配质量及效率,降低了粉尘污染。
(2)机身部件3段对合与精加工系统。
该系统用于实现机身数字化调姿、对合,机翼/垂尾调姿,机身、机翼交点孔/面精加工,机器人辅助系统件安装和测量点打制等,是国内第一套集激光检测数据采集、自动控制、数控加工、机器人应用、集成控制等技术为一体的复杂数字化装配系统。
(3)机翼数字化装配系统。
该系统用于实现飞机机翼数字化定位和自动化制孔,以达到提高壁板定位和装配协调准确度,提高制孔质量和效率的目标。
(4)机翼-机身、垂尾-机身对合系统。
该系统具有高负载、高精度的位置和姿态调整功能,同时具有装配过程的可视化监控功能、并能实时监控装配过程中的装配压紧以避免发生碰撞,有效解决了传统人工装配方式中装配精度主要取决于工人的经验,装配质量难以得到控制、装配可靠性差、工作强度大、安全隐患大、效率低下的问题。
(5)全机数字化水平测量与校准系统。
该系统采用基于iGPS和激光雷达的数字化水平测量与校准技术,可在飞机自然摆放状态下对飞机进行水平测量与校准,省略了飞机调平这一繁琐工序,并降低或消除由于飞机基准点测量误差和调平误差所引入的水平测量和校准误差。
结束语
数字化装配技术代表了当今飞机制造的发展方向,涉及多学科如新材料、通信、机械、计算机、控制、电子等领域的综合研究与应用,其研究必须与工艺技术、实验技术、检测技术和现代管理等技术的研究相结合,以实现生产模式和方法的转变。在现阶段,我国数字化装配技术的研究和应用还受到如下因素的制约:
(1)基础工业水平薄弱导致的各类先进数控设备缺乏。
目前,由于国内基础工业制造水平的限制,各类高精度的数控制孔、自动钻铆、激光测量等数字化装配关键设备仍需进口。国内航空企业应结合自身应用需求,积极主动地与高校及科研院所开展联合攻关,逐步开发出具有自主知识产权的数字化配套设备与工装。
(2)传统装配观念的限制。
由于历史的原因,国内航空企业受到前苏联的飞机生产组织模式影响较深,很多设计及工艺人员甚至组织者的装配观念还停留在几十年来形成的手工作业和串行生产模式,因此亟需广大设计及工艺人员尽快完成从传统装配观念到先进的数字化装配理念的转变,主动学习并消化先进的数字化装配技术,并在生产实践中摸索出适合我国国情的技术革新之路。
(3)行业标准尤其是数字化装配标准规范体系缺乏。
近年来国内航空企业对数字化装配技术已进行了不同程度的探索,但还远远不足以构成整个行业的标准体系,因此亟需建立一套与国情相适应的数字化装配标准规范体系,指导各单位建立基于产品属性和配置规则的单一数据源,形成以产品数据模型为基础,各部门协同作业的标准综合组织生产模式。
(4)资金和场地的限制。
数字化装配技术的研究和应用是高投入的长期投资,需要大量和持续的资金投入,不能期望一蹴而就,同时为了实现合理优化的数字化装配系统工艺布局,还需场地空间的充分保证。
综上所述,数字化装配技术代表了现代飞机制造的发展方向,其研究和应用既是技术的革命,又是观念的革命,更是管理的革命。深入研究并逐步应用数字化装配技术,在提升产品质量和生产效率的同时,更能促进我国航空产品生产的观念性改变及管理体制的变革,攻克我国飞机装配及制造技术中的薄弱环节,实现飞机制造技术水平的重大突破。